- Muratec Sustainability
- Environment
- Health and Safety
- Occupational Health and Safety Policy
- Approach to Occupational Health and Safety
- Health and Productivity Management
- Human Rights
- Together with Local Communities
- Governance
Products
- Home
- Sustainability
- Approach to Occupational Health and Safety
Approach to Occupational Health and Safety
The Muratec Group makes protecting the health and safety of its employees a top management priority. We have established our safety and health policy to realize a safe and comfortable working environment and promote the mental and physical health of our employees. That’s why we have established an occupational safety and health management system headed by the president and CEO. The safety and health committee of each business site carries out their own actions while the EHS Committee, based out of the head office, implements group-wide initiatives with an eye to making continuous improvements.
ISO 45001 certification
The Inuyama Health and Safety Site(*1) based at the Inuyama Plant acquired ISO 45001 certification, an international standard for occupational health and safety management systems, in March 2021. Through risk assessments and legal compliance evaluations, as well as annual internal audits and management reviews, we aim to continuously improve our activities and eliminate occupational accidents.
*1 Inuyama Plant (including affiliated companies), Ise Factory, Toyohashi Factory, and Murata Tool Gifu Factory
We strive to prevent occupational and traffic accidents by identifying and improving dangerous areas through risk assessments and near misses, and by raising safety awareness through education and awareness activities. We also set numerical targets according to the issues faced by each business site, and manage performance and achievement rates.
Risk assessment
We have deployed risk assessment and legal compliance evaluation methods and forms in accordance with ISO45001 to our major business sites to identify and reduce risks and ensure compliance with the latest laws and regulations.
Safety and health notebook
We distribute pocket-sized "safety and health handbooks" containing safety and health rules to all employees, and provide training at the time of distribution. We are working to improve each employee's safety and health awareness by reading each page one by one during morning and lunch meetings.
Labor-management safety patrol
Each year, the president, vice presidents, officers, and labor union inspect major worksites. The goal is to improve overall health and safety by identifying problems from a company-wide perspective. This approach differs from the daily patrols carried out at each worksite.
Employee training
Various types of education and training are provided to prevent industrial accidents and traffic accidents.
Safety and discipline education
Facilities are set up at each plant to provide safety education by simulating the hazards that may be present in the workplace.
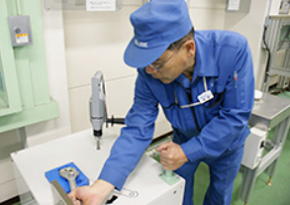
Traffic safety course
Once a year, we conduct a course on the importance of traffic safety based on videos of traffic accidents and near-misses.
Industrial accidents
When an industrial accident occurs, we identify the conditions of people, equipment, and the management system at the time of the accident, analyze the cause of the accident, and take countermeasures. To prevent similar accidents from occurring, we maintain a centralized record of past accidents and make it available to employees.
Number of industrial accidents *1
(Year ending March)
2020 | 2021 | 2022 | 2023 | 2024 | |
---|---|---|---|---|---|
Lost-time injuries (1day or more of lost time) |
6 | 1 | 2 | 4 | 3 |
Non lost-time injuries (less than 1day of lost time) |
12 | 13 | 14 | 15 | 12 |
(Number of occurrences)
*1 All employees of the Muratec Group who work at its major locations (Head Office/Inuyama/Ise/Kaga/Muratec Mechatronics Co., Ltd. Shiga/Oita) including temporary employees but excluding employees of contractors
Frequency rate of lost-time injury

* The number of lost-time injuries that occurred in a workplace per million hours worked, a measure for the frequency of work-related injuries
* Japanese manufacturing industry average is quoted from the Ministry of Health, Labor and Welfare's occupational accident trend survey
Severity rate of lost-time injury

* The number of lost workdays per 1,000 hours worked, a measure for the severity of work-related injuries
* Japanese manufacturing industry average is quoted from the Ministry of Health, Labor and Welfare's occupational accident trend survey